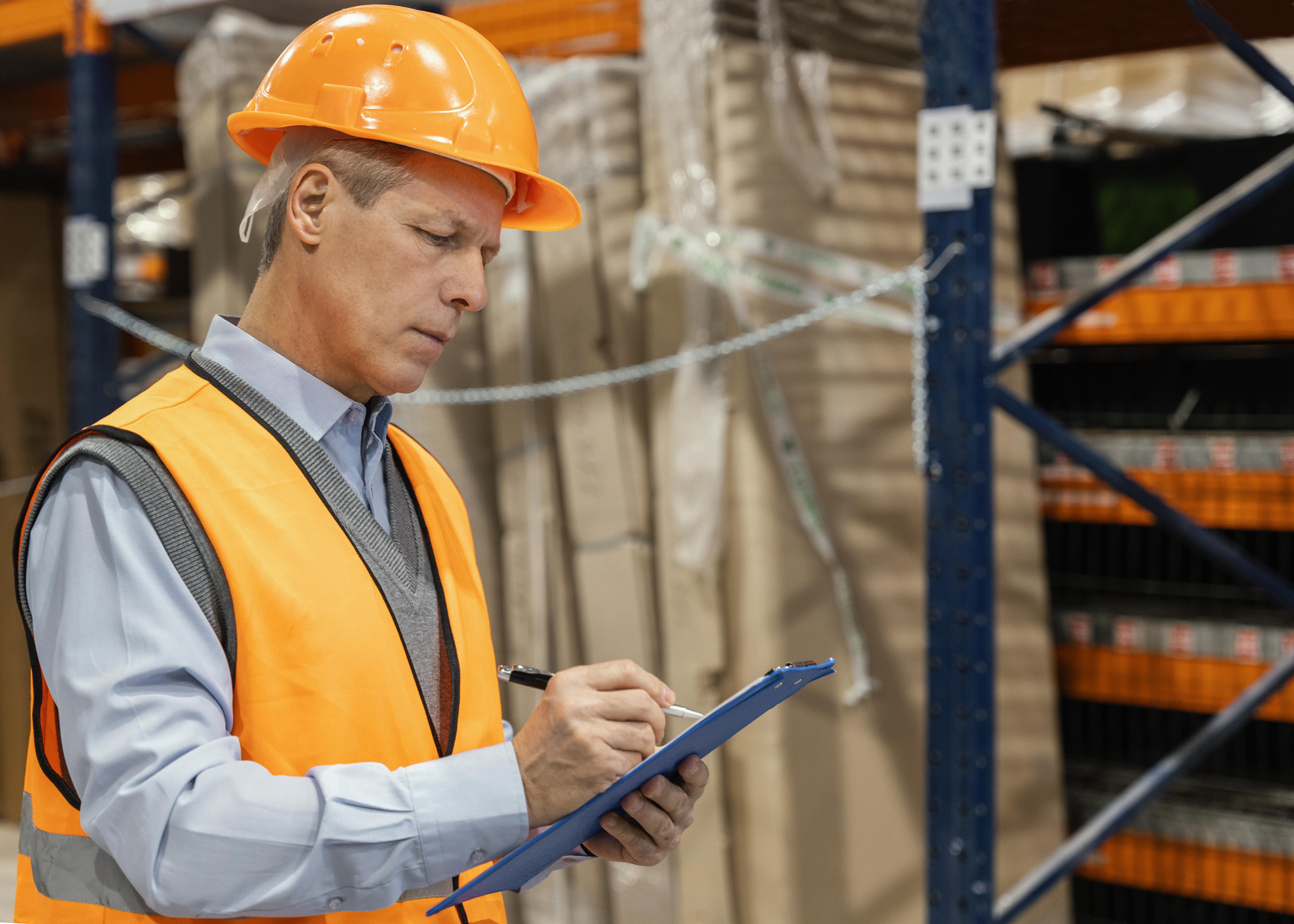
The Role of Inventory Management
The Role of Inventory Management
For small manufacturing businesses with limited stock, small warehouse spaces, and few customer orders, managing inventory with spreadsheets may suffice. However, in larger, more complex environments, a more advanced inventory management system is required, one that collects, processes, manages, and generates reports on all data in real-time. Failing to track each incoming and outgoing item can significantly affect cash flow. Therefore, inventory management is crucial for any growing manufacturing company.
The role of inventory management is to ensure that inventory is maintained at a level that meets the company's needs. It serves several purposes, including:
- Monitoring the quantity, accuracy, and quality of inventory;
- Supporting compliance with legal requirements through traceability;
- Optimizing ordering and replenishment processes;
- Ensuring the right inventory is in the right location to maintain customer service levels;
- Controlling the movement and distribution of inventory;
- Evaluating and managing warehouse costs;
- Providing control points.
Advantages of an Inventory Management System
- Keeping inventory at optimal levels and in the correct locations;
- Enabling more accurate inventory management;
- Reducing losses, obsolescence, and excess stock;
- Improving order fulfillment and timely delivery;
- Preventing production stoppages due to inventory shortages;
- Making stock counts more efficient;
- Providing data that improves procurement and replenishment processes;
- Increasing transparency of inventory data and enabling more informed decision-making.
Inventory Optimization
The main challenge for manufacturers is to keep the required stock at a minimum while providing the "right amount." The primary goal is to find optimal inventory levels. Inventory Optimization (IO) advances inventory management by evaluating various relevant signals within the supply chain. This helps the company forecast inventory levels to maximize profits while minimizing waste. IO assists in selecting the best stock-keeping and reordering strategies for each product group or inventory set.
Key activities include:
- Analyzing inventory by importance and behavior, and classifying them into similar groups;
- Creating demand forecasts for each inventory item with high forecast accuracy as the main goal;
- Modeling the impact of inventory strategies and checking if these strategies improve service levels;
- Replenishing inventory based on forecasts and inventory strategies.
Technical Requirements for Optimization
To achieve optimal inventory levels, accurate and timely data is essential. These requirements are often not met when spreadsheets or independent applications are used. Integrating inventory planning and optimization into an ERP system significantly reduces these issues. IO is not a one-time process. It is an interdisciplinary process that requires continuous review and improvement, but it offers significant profit potential.
The Need for Inventory Management and Optimization
Effective inventory management should be a priority for every manufacturing business and thus an essential part of an ERP system. This provides the company with a unified real-time view of its inventory. This detailed real-time data is crucial for efficient customer service and effective management. In an uncertain business environment, where liquidity and customers are the primary concerns, an inventory optimization project is a worthwhile investment to improve working capital and customer service levels.